New 3D Printed CubeSat from Roboze and University of Colorado Boulder's Aerospace Team Measures Electromagnetic Effects of Space Storms
CubeSat will spend six months in orbit measuring electromagnetic lightning waves with components produced with Roboze 3D printing technology
Today Roboze, a manufacturer of industrial 3D printing technology for extreme end-use applications, announced it has been selected by the University of Colorado Boulder to optimize the design and 3D printed components for a CubeSat project within the college's department of Aerospace Engineering Sciences. The CubeSat will spend at least six months in orbit measuring electromagnetic waves emitted by lightning discharges on the earth's surface.
The CubeSat's small size and particular geometries, including strict mass and volume limitations, prompted the Lightning, Atmosphere, Ionosphere and Radiation Belt (LAIR) research team to select 3D printing over conventional methods for the manufacturing of critical components. Leveraging its high-performance polymer, polyether ether ketone (PEEK), Roboze will produce the CubeSat's magnetic field sensor holders.
"Because we are so constrained by mass, 3D printing was the ideal solution for our CubeSat," said Vicki Knoer, a researcher in the project. "Roboze allowed us to meet the requirements of the project by guiding us in choosing the most suitable material and in the optimization of the parts to minimize mass. We are very satisfied with the results we are achieving."
The project kicked off in spring 2019, and after the first validation phases, it will see the launch into space in the first half of 2022.
"Thanks to extraordinary mechanical properties as well as high thermal and chemical resistance, 3D printing is rapidly replacing metal in a wide variety of extreme end-use applications including aerospace, mobility and energy," said Roboze founder and CEO Alessio Lorusso. "It was an honor and a real privilege to collaborate with the LAIR group on this project. They are one of the pioneers in the use of additive technology in this field and giving our support to the realization of their mission makes me extremely proud."
About Roboze
Roboze is re-shaping the manufacturing industry and revolutionizing the world of 3D printing with the most precise technology, capable of processing super polymers and composite materials on-demand for finished functional parts for extreme applications in the aerospace, oil and gas, energy, manufacturing and mobility sectors. The Roboze high technical ecosystem includes a complete range of advanced 3D printers for high temperature and high strength super plastics, developed with the collaboration of the best global players. It guarantees a real optimization of costs and time along the entire supply chain, while bringing additive manufacturing closer to the standards of traditional manufacturing. To date, Roboze is used in more than 25 countries globally and recognized as one of the fastest-growing 3D printing companies in the world, serving industry leaders like GE, Leonardo, the U.S. Army and many others.
Featured Product
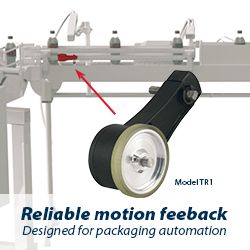