GE Additive welcomes Sandvik into Binder Jet Beta Partner Program
GE Additive’s Binder Jet beta partner program leverages the company’s strength in industrializing additive technology with strong technical and innovative partners to rapidly grow its Binder Jet technology. The first phase involves developing the beta H2 system into pilot lines, and eventually into a commercially available factory solution in 2021.
Cincinnati, OH, October 12, 2020 - GE Additive has announced that Sandvik Additive Manufacturing has become a strategic partner in its Binder Jet beta partner program. Sandvik has one of the widest alloy program for additive manufacturing on the market, marketed under the Osprey® brand.
GE Additive's Binder Jet beta partner program leverages the company's strength in industrializing additive technology with strong technical and innovative partners to rapidly grow its Binder Jet technology. The first phase involves developing the beta H2 system into pilot lines, and eventually into a commercially available factory solution in 2021.
"Our approach to Binder Jet is making additive mass production a reality in every industry. And while it would be relatively easier to launch individual machines, we continue to hear from customers, especially in the automotive industry, that they need a complete solution that can scale." said Jacob Brunsberg, Binder Jet product line leader, GE Additive.
"Attracting partners like Sandvik - with know-how in industrializing innovation, deep materials knowledge, and a shared vision for the potential for additive technology - remains a cornerstone of our Binder Jet commercialization strategy," he added.
"Sandvik is a leading expert in gas-atomized additive manufacturing powders, as well as in optimizing the materials to customers' specific print processes and applications," said Kristian Egeberg, President of Sandvik Additive Manufacturing. "The materials collaboration with GE Additive offers great opportunities to qualify our wide range of Osprey® metal powders for their new Binder Jet platform, to enhance end customer productivity and product performance."
Sandvik brings the program over 150 years of leading expertise in materials technology, more than 40 years experience of powder atomization, leading know-how in post processing methods such as metal cutting, sintering and heat treatment, and extensive expertise across the entire additive technology value chain - from metal powder to finished additive components.
In 2019, Sandvik acquired a significant stake in BEAMIT, a leading European-based AM service bureau, and in 2020 the BEAMIT Group acquired 100% of ZARE, bringing together two leading AM service bureaus in Europe - to create one of the largest independent AM service providers, serving the most demanding industries.
Featured Product
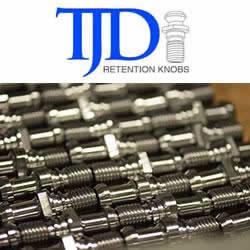