Aubert & Duval and Alloyed to host Webinar on July 1st on New Material ABD®-900AM for Metal Additive Manufacturing
(June 18th, 2020) Material developments are vital as industry moves to use metal additive manufacturing (AM) in an array of demanding and often safety critical applications.
(June 18th, 2020) Material developments are vital as industry moves to use metal additive manufacturing (AM) in an array of demanding and often safety critical applications.
Aubert & Duval — a world leader in high-performance steel, superalloy, aluminium or titanium parts and metal powders — and Alloyed (formerly OxMet Technologies) — which delivers next generation performance for metal components through its unique stack of technologies — will be hosting a Webinar on July 1st 2020 focussing on ABD®-900AM innovative material for additive manufacturing.
ABD®-900AM is an age-hardenable Ni-based superalloy created specifically for the demands of AM. The alloy was designed to provide an improved combination of high strength, high creep- and oxidation-resistance, and excellent manufacturability compared with alloys commonly used for AM. This has been confirmed by performance assessment on ABD-900AM using laser powder bed fusion (LPBF). The printability of the alloy using LPBF shows a high resistance to cracking and ~99.9% density.
Designed for use at high temperatures up to 900°C / 1650°F, ABD®-900AM has been tailored for AM by Alloyed not just for high mechanical properties, but also for excellent printability. Compared with Ni718, ABD®‑900AM provides a minimum of 30% improvement in yield stress at temperatures >800°C and a creep temperature capability improvement by up to 150oC - similar to alloy 939 and alloy 738.
Will Dick-Cleland, Additive Manufacturing Engineer at Alloyed, and Adeline Riou, Global Sales Manager at Aubert & Duval will provide an overview of material properties as well as various case studies of interest for space, aircraft engines, gas turbines, and motorsports.
The Webinar will last 30 minutes, and is free to attend. It will begin Wednesday July 1st 2020 at 17.00 Central Europe Time (UTC+2). You can register for the Webinar at https://aubertetduval-esj.my.webex.com/mw3300/mywebex/default.do?service=1&siteurl=aubertetduval-esj.my-en&nomenu=true&main_url=%2Fmc3300%2Fe.do%3Fsiteurl%3Daubertetduval-esj.my-en%26AT%3DMI%26EventID%3D1014125077%26UID%3D0%26Host%3DQUhTSwAAAASo9LtbjNs-q5HGtePaxRsOG3wW6jUDY-TmDmHYU_OuEpiDLvHxp8qz68BHSa-aPP9cLcTR8j-eC53VOiHVXVQ70%26RG%3D1%26FrameSet%3D2%26RGID%3Dr732ef2667b4db4e0f84c3dc9e0133b95
Featured Product
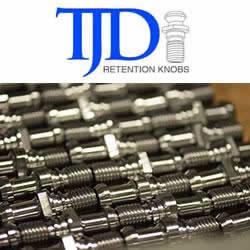
T.J. Davies' Retention Knobs
Our retention knobs are manufactured above international standards or to machine builder specifications. Retention knobs are manufactured utilizing AMS-6274/AISI-8620 alloy steel drawn in the United States. Threads are single-pointed on our lathes while manufacturing all other retention knob features to ensure high concentricity. Our process ensures that our threads are balanced (lead in/lead out at 180 degrees.) Each retention knob is carburized (hardened) to 58-62HRC, and case depth is .020-.030. Core hardness 40HRC. Each retention knob is coated utilizing a hot black oxide coating to military specifications. Our retention knobs are 100% covered in black oxide to prevent rust. All retention knob surfaces (not just mating surfaces) have a precision finish of 32 RMA micro or better: ISO grade 6N. Each retention knob is magnetic particle tested and tested at 2.5 times the pulling force of the drawbar. Certifications are maintained for each step in the manufacturing process for traceability.