3D Printing Powder Optimization is Key to Part Quality, Productivity
GEMCO will demonstrate how refining powder characteristics like flow can enhance part quality, consistency, repeatability and productivity at the RAPID + TCT Additive Manufacturing Conference from April 20-23, 2020 at the Anaheim Convention Center in Anaheim, CA, Booth #1139.
GEMCO will demonstrate how refining powder characteristics like flow can enhance part quality, consistency, repeatability and productivity at the RAPID + TCT Additive Manufacturing Conference from April 20-23, 2020 at the Anaheim Convention Center in Anaheim, CA, Booth #1139.
GEMCO, a Middlesex, NJ-based manufacturer of tumble blending and vacuum tumble-drying equipment, founded in 1916, is a technical expert on powders. This includes understanding powder chemistry, physical attributes, and how powders will interact when blended.
The global 3D printing metals market is growing and expected to reach USD 3.05 billion by 2025, according to a recent report by Grand View Research, Inc. However, to take full advantage of this growth and efficiently produce high-quality parts, powder producers, 3D printer manufacturers and others will need to ensure the consistent, repeatable quality of the metal powders used in the process.
Although there is a wide range of metal powder suppliers, the industry is turning to experts in powder processing for sophisticated blending and heat treatments that improve the quality of the powder. As 3D printing techniques and equipment continue to advance, optimizing the powders in this way can improve powder flowability to prevent clogging, speed the process and produce a higher-quality part.
At the show, the company also plans to exhibit its new Transparent Powder Mixer, which offers the industry's fastest, clearest insight into mixing. Its clear acrylic mixing shell provides full transparency into the real-time state of powder blending, which enables researchers to fast-track the final product and process. Offered with a fully transparent double cone, the lab mixer is a scaled down version of a full production unit with similar PLC controls.
For more info, call 800-654-3626 in the U.S.; Fax 732-733-1175; email sales@okgemco.com; visit okgemco.com; or write to GEMCO at 301 Smalley Ave, Middlesex, NJ 08846 USA.
Featured Product
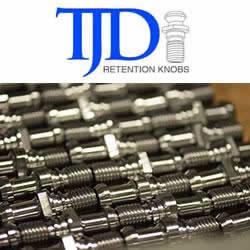
T.J. Davies' Retention Knobs
Our retention knobs are manufactured above international standards or to machine builder specifications. Retention knobs are manufactured utilizing AMS-6274/AISI-8620 alloy steel drawn in the United States. Threads are single-pointed on our lathes while manufacturing all other retention knob features to ensure high concentricity. Our process ensures that our threads are balanced (lead in/lead out at 180 degrees.) Each retention knob is carburized (hardened) to 58-62HRC, and case depth is .020-.030. Core hardness 40HRC. Each retention knob is coated utilizing a hot black oxide coating to military specifications. Our retention knobs are 100% covered in black oxide to prevent rust. All retention knob surfaces (not just mating surfaces) have a precision finish of 32 RMA micro or better: ISO grade 6N. Each retention knob is magnetic particle tested and tested at 2.5 times the pulling force of the drawbar. Certifications are maintained for each step in the manufacturing process for traceability.