B&W MEGTEC Introduces the GigaCoater™ for Lithium-Ion Battery Electrodes
New wide-web coating system uses simultaneous 2-sided process to produce up to 3 GWhr of battery electrode output annually, creating enough capacity for 30,000 electric vehicles configured for 100 kWh or 5 hours of backup power for 300,000 homes based on average consumption of 2 kWh.
B&W MEGTEC Introduces the GigaCoater™ for Lithium-Ion Battery Electrodes
New wide-web coating system uses simultaneous 2-sided process to produce up to 3 GWhr of battery electrode output annually
(De Pere, Wis. - Sept. 12, 2017) Babcock & Wilcox MEGTEC (B&W MEGTEC), a subsidiary of Babcock & Wilcox Enterprises, Inc., has launched the GigaCoater™ wide-web coating line for lithium-ion battery electrodes.
Developed to provide high-volume production of battery electrodes, each GigaCoater can produce up to 3 GWhr of electrode per year on average. The GigaCoater coating platform utilizes B&W MEGTECs exclusive simultaneous 2-sided coating system.
"The energy storage industry is demanding a significant reduction in production costs in combination with increased yields and product quality," said Jeff Quass, vice president of technology and development, B&W MEGTEC. "The GigaCoater offers increased foil width and faster speeds. Coupled with our simultaneous two-sided coating system, the GigaCoater provides a simplified coating line that approximately doubles manufacturing capacity within the same footprint as a single-side sequential line."
The dual-coating method, in combination with coating rheology and GigaCoater machine properties, maximizes production time and delivers in-line quality control. Additional GigaCoater specifications include:
• Web width of 1,300 mm
• Coating width of 1,200 mm
• Mechanical speed of 50/m/min
• Process speed of 40 m/min
• Wet coat weight of up to 400 gsm/side
"Manufacturing large quantities of lithium-ion battery cells requires a significant change and dimensional up-scaling of the production equipment and output per line to achieve industry targets," Quass notes. "At the same time, the benefits of two-sided simultaneous coating technology become increasingly important the wider and faster coating lines are required to get."
The GigaCoater maximizes manufacturing at a significantly lower total production cost with:
• 50 percent to 70 percent less floor space than typical single-side coating operations, which allows for more efficient plant layouts
• Thermal efficiencies that deliver lower energy requirements
• A wide-web width that significantly reduces the number of coils needing to be handled
• Simplified material flow that enhances overall throughput
• Higher automation that maximizes production volume
About B&W MEGTEC
Babcock & Wilcox MEGTEC, a subsidiary of Babcock & Wilcox, designs, engineers, manufactures and services sophisticated air pollution control systems, and coating and drying equipment for the industrial sector.
About B&W
Headquartered in Charlotte, N.C., Babcock & Wilcox is a global leader in energy and environmental technologies and services for the power and industrial markets, and has been transforming our world for 150 years. B&W companies employ approximately 5,000 people worldwide. Follow us on Twitter @BabcockWilcox and learn more at www.babcock.com.
Featured Product
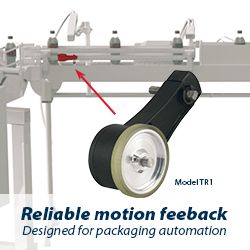
Model TR1 Tru-Trac
The Model TR1 Tru-Trac® linear measurement solution is a versatile option for tracking velocity, position, or distance over a wide variety of surfaces. An integrated encoder, measuring wheel, and spring-loaded torsion arm in one, compact unit, the Model TR1 is easy to install. The spring-loaded torsion arm offers adjustable torsion load, allowing the Model TR1 to be mounted in almost any orientation - even upside-down. The threaded shaft on the pivot axis is field reversible, providing mounting access from either side. With operating speeds up to 3000 feet per minute, a wide variety of configuration options - including multiple wheel material options - and a housing made from a durable, conductive composite material that minimizes static buildup, the Model TR1 Tru-Trac® is the ideal solution for countless applications.