Predator3D™ Bead Inspection Auto Repair Function Released
Coherix, Inc., a global leader in Three-Dimensional (3D) Machine Vision, today announced a new capability for its Predator3D bead inspection solution. This new feature enables Predator3D to automatically repair an incorrectly dispensed bead.
Coherix, Inc., a global leader in Three-Dimensional (3D) Machine Vision, today announced a new capability for its Predator3D bead inspection solution. This new feature enables Predator3D to automatically repair an incorrectly dispensed bead. If Predator3D detects that a section of the bead is defective and repairable during the dispensing process, it instructs the robot to perform a repair pass following the same path as a normal dispense but allows Predator3D to control the bead dispenser. Predator3D will then turn the dispenser on at specific locations in order to repair the bead. It will also inspect during the repair pass to verify that the repair was successful.
Predator3D automatic repair feature is easy to set up, and can be done on any robot or PLC protocol. Predator3D automatic repair feature will be part of the Predator3D standard package and this feature is retroactively compatible with field systems.
Coherix Predator3D bead inspection is by far the most advanced structural adhesive and sealant bead inspection solution in the market. The company also provides a series of inline Robust3D™ error proofing solutions, such as engine piston assembly verification, rolling finger follower assembly inspection, valve assembly verification, and flexible end-of-line inspection, as well as combustion chamber volume measurement.
For more information about Coherix Predator3D automatic repair function, please call Coherix at (734) 922-4070 or email coherixinfo(at)coherix.com.
About Coherix, Inc.
Coherix, Inc. develops and manufactures high-speed, high-definition 3D machine vision products that enable our customers to manage high-volume precision manufacturing processes. Coherix products are designed for inspection and error-proofing in the automotive, semiconductor, and electronics industries. Coherix is committed to producing the highest performing 3D machine vision products at the lowest Total Cost of Ownership. Coherix customers and partners include global end users, system integrators, and distributors, who demand 100 percent reliability that Coherix products provide. Headquartered in Ann Arbor, Michigan, the company has offices in the United States, China, Germany, Singapore, and Japan.
Featured Product
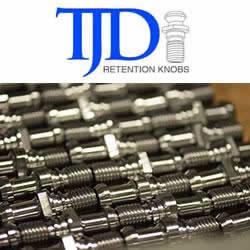