Materialise 3D Printing Solutions Improve Pediatric Care in U.S.
These 3D-printed guides, when used in coordination with 3D pre-operative planning, help surgeons improve planning processes to increase confidence both before and during the surgery that the desired outcome will be obtained.
PLYMOUTH, Mich.--(BUSINESS WIRE)--Imagine a child who wants to run and throw a ball with their friend, but due to a bone deformity, theyre unable to participate and must instead watch from the sidelines. No longer does that child need to be sidelined, Materialise (NASDAQ:MTLS) has clearance for 3D-printed patient-specific radius and ulna osteotomy guides for children as young as seven years to help orthopaedic surgeons understand and execute even the most complex cases. These 3D-printed guides, when used in coordination with 3D pre-operative planning, help surgeons improve planning processes to increase confidence both before and during the surgery that the desired outcome will be obtained.
Prior to this new FDA clearance, pediatric osteotomy planning was done using X-ray images to draw freehand surgical plans. Whether caused by trauma or natural-occurring, a deformity in the upper extremities in children can be difficult to fully visualize and plan for, and in cases where a child has lost the ability to rotate their forearm, surgical correction can be quite challenging. No matter how skilled the surgeon or how much planning goes into preparation, there was always a level of uncertainty when relying on a freehand model. In fact, approximately 60 percent of osteotomies, in the distal-radius actually never obtained the planned correction. With this new clearance that will change for children 7 years and older. Advances in medical 3D printing by Materialise allow the creation of patient-specific guides at a reasonable cost.
"In bringing this 3D printing technology to pediatric surgery, surgeons will have access to our clinical engineers wealth of experience developing osteotomy guides, helping them perform even the most complex bone corrections that will have a positive impact on the rest of the childs life," said Bryan Crutchfield, Vice President and General Manager Materialise North America.
With more than 1,000 clinical osteotomy consultations with adult patients under their belt, Materialise is able to provide their expertise in 3D-printed surgical planning for operations on children ages seven and up. Each 3D printed surgical guide, created by Materialise in collaboration with the surgeon, is patient-specific and designed to fit uniquely on the bone of the patient leading to a more predictable outcome.
In complex cases, like one in the UK, surgeons can work directly with Materialise Clinical Engineers to help guide them through the process and produce the best osteotomy guide available for that child. Because each guide is patient-specific, they are uniquely able to handle these complex cases and have in some cases been used to perform first of their kind corrections.
In the United Kingdom, a young man underwent surgery on a routine wrist fracture, but following the procedure he suffered complications due to further bone deterioration and would need additional surgery to repair the damage and alleviate his pain. Materialise scanned both his healthy and fractured wrist and were able to plan the optimal cuts to be made by the surgeon and designed surgical guides for his unique case. This first of its kind surgery was successful and no further complications have appeared.
This pioneering procedure can now be applied to children seven years and older, and can give them hope that no matter how complex their case may be, they dont need to be sidelined forever. They can be playing with their friends and living a normal life thanks to this 3D printed solution.
Materialise has worked closely with surgeons and hospitals around the world for nine years to develop and refine the process to implement 3D-printed osteotomy guides in complex bone corrections in adults. In expanding this technology to children, Materialise hopes to directly contribute to better and healthier lives for them.
Materialise has leveraged more than 26 years of experience in the 3D printing industry to develop software and services that act as the backbone of 3D printing solutions, helping partners in the healthcare, technology and manufacturing industries implement 3D-printed solutions for their customers and working with medical professionals to help them efficiently develop and implement solutions to improve access to the cost-saving, patient specific benefits of 3D printing.
Materialises full range of end-to-end 3D printing solutions for the orthopaedic industry, including surgical planning software and patient-specific medical devices, are on display at booth #5423 at the AAOS Annual meeting through March 17, 2017.
About Materialise
Materialise incorporates more than 26 years of 3D printing experience into a range of software solutions and 3D printing services, which together form the backbone of 3D printing technologies. Materialises open and flexible solutions enable players in a wide variety of industries, including healthcare, automotive, aerospace, art and design, and consumer goods, to build innovative 3D printing applications that aim to make the world a better and healthier place. Headquartered in Belgium, with branches worldwide, Materialise combines the largest group of software developers in the industry with one of the largest 3D printing facilities in the world. For additional information, please visit: www.materialise.com.
Featured Product
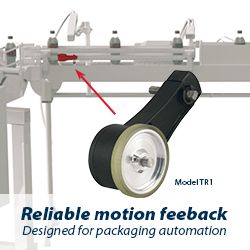