Transforming Semiconductor Manufacturing: Connecting SC-80EX to SECS/GEM with EIGEMBox for Enhanced Integration
Enhancing Efficiency and Automation in Semiconductor Manufacturing In the fast-paced world of semiconductor manufacturing, efficiency and reliability are paramount. As technology continues to advance, the demand for smarter solutions to streamline processes and improve productivity grows ever stronger. One such solution that has been making waves in the industry is the integration of SECS/GEM protocol with cutting-edge equipment like the SC-80EX, facilitated by innovative platforms such as the EIGEMBox.
we delve into the significance of SECS/GEM integration, explore how it transforms the capabilities of the SC-80EX, and discuss the pivotal role of the EIGEMBox in facilitating seamless communication and data exchange.
Understanding SECS/GEM Integration
SECS/GEM (SEMI Equipment Communications Standard/Generic Equipment Model) is a standardized communication protocol widely adopted in the semiconductor industry. It allows for efficient data exchange between manufacturing equipment and host systems, enabling real-time monitoring, control, and optimization of manufacturing processes. By integrating SECS/GEM into equipment like the SC-80EX, manufacturers can achieve greater visibility, traceability, and control over their production lines.
The Power of the SC-80EX
The SC-80EX is a state-of-the-art semiconductor manufacturing tool known for its precision, reliability, and advanced functionality. By integrating SECS/GEM protocol with the SC-80EX, manufacturers can unlock a myriad of benefits, including:
Enhanced Data Exchange: SECS/GEM integration enables seamless communication between the SC-80EX and other equipment or host systems on the manufacturing floor, allowing for real-time data exchange and synchronization.
Improved Process Control: With SECS/GEM integration, manufacturers can remotely monitor and control the operation of the SC-80EX, ensuring optimal performance and minimizing downtime.
Streamlined Workflow: By automating data collection, reporting, and analysis tasks, SECS/GEM integration simplifies workflow management, allowing manufacturers to focus on value-added activities and decision-making.
Compliance and Traceability: SECS/GEM integration facilitates compliance with industry standards and regulations by providing a standardized framework for data exchange and documentation. It also enhances traceability by recording detailed process information and event logs.
The Role of EIGEMBox
At the heart of SECS/GEM integration lies the EIGEMBox, a sophisticated communication gateway that serves as a bridge between the SC-80EX and external systems. The EIGEMBox plays a crucial role in facilitating seamless data communication, protocol conversion, and message routing, ensuring compatibility and interoperability across diverse manufacturing environments.
Unlocking the Potential
By harnessing the power of SECS/GEM integration with the SC-80EX through the EIGEMBox, semiconductor manufacturers can unlock the full potential of their production lines. From optimizing process efficiency and productivity to ensuring compliance and traceability, this innovative solution empowers manufacturers to stay ahead in today's competitive market landscape.
Take the Next Step with EIGEMBox
Ready to revolutionize your semiconductor manufacturing operations? Contact us today to learn more about SECS/GEM integration with the SC-80EX and discover how the EIGEMBox can drive efficiency, reliability, and innovation in your production processes.
Experience the power of SECS/GEM integration with the SC-80EX. Contact us today to schedule a demo and take your semiconductor manufacturing to new heights.
Featured Product
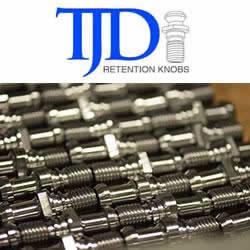