Revolutionizing Semiconductor Manufacturing with Automated Optical Inspection Software
In the dynamic world of semiconductor manufacturing, precision and efficiency are paramount. Every detail matters, from the design phase to the final product. This is where Automated Optical Inspection (AOI) software steps in as a game-changer, revolutionizing the industry and ensuring quality control at every stage.
Introduction:
As the demand for smaller, faster, and more powerful semiconductor devices continues to rise, manufacturers are under immense pressure to deliver flawless products while maintaining cost-effectiveness. Traditional manual inspection methods are no longer sufficient to meet these demands. Enter Automated Optical Inspection (AOI) software - a sophisticated solution that leverages advanced imaging technology and intelligent algorithms to streamline the inspection process and enhance overall efficiency.
The Role of AOI Software in Semiconductor Manufacturing:
Enhanced Accuracy: AOI software utilizes high-resolution imaging systems to detect even the tiniest defects in semiconductor components. From surface abnormalities to solder joint integrity, no detail goes unnoticed, ensuring unparalleled accuracy in inspection results.
Increased Efficiency: By automating the inspection process, AOI software significantly reduces the time and resources required for quality control. What once took hours or days to inspect manually can now be completed in a fraction of the time, allowing manufacturers to optimize their production cycles and meet tight deadlines.
Real-time Analysis: AOI software provides real-time feedback on inspection results, enabling manufacturers to identify and address issues promptly. This proactive approach minimizes the risk of defects propagating through the production line, ultimately saving time and resources.
Adaptability: With customizable inspection criteria and parameters, AOI software can adapt to the unique requirements of different semiconductor applications. Whether inspecting PCBs, wafer substrates, or individual components, the software can be tailored to suit specific manufacturing processes.
Key Features of AOI Software:
Defect Detection Algorithms: Advanced algorithms analyze captured images to identify defects such as scratches, cracks, soldering issues, and misplaced components with unparalleled accuracy.
Machine Learning Integration: Some AOI software solutions incorporate machine learning capabilities, allowing the system to continuously improve its defect detection algorithms based on historical data and user feedback.
Integration with Manufacturing Systems: Seamless integration with existing manufacturing systems enables automated data exchange, streamlining the workflow and eliminating the need for manual data entry.
Customizable Reporting: AOI software generates comprehensive inspection reports, complete with images, annotations, and statistical data, empowering manufacturers to make informed decisions and track quality trends over time.
Conclusion:
In an industry where precision and reliability are non-negotiable, Automated Optical Inspection software emerges as a game-changer for semiconductor manufacturers worldwide. By harnessing the power of advanced imaging technology and intelligent algorithms, AOI software not only enhances the quality control process but also drives efficiency, productivity, and innovation across the semiconductor manufacturing ecosystem. As technology continues to evolve, embracing AOI software is no longer an option but a necessity for staying ahead of the curve in the competitive semiconductor market.
Featured Product
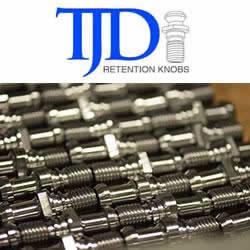
T.J. Davies' Retention Knobs
Our retention knobs are manufactured above international standards or to machine builder specifications. Retention knobs are manufactured utilizing AMS-6274/AISI-8620 alloy steel drawn in the United States. Threads are single-pointed on our lathes while manufacturing all other retention knob features to ensure high concentricity. Our process ensures that our threads are balanced (lead in/lead out at 180 degrees.) Each retention knob is carburized (hardened) to 58-62HRC, and case depth is .020-.030. Core hardness 40HRC. Each retention knob is coated utilizing a hot black oxide coating to military specifications. Our retention knobs are 100% covered in black oxide to prevent rust. All retention knob surfaces (not just mating surfaces) have a precision finish of 32 RMA micro or better: ISO grade 6N. Each retention knob is magnetic particle tested and tested at 2.5 times the pulling force of the drawbar. Certifications are maintained for each step in the manufacturing process for traceability.