Artificial Intelligence has emerged as a transformative force in industry. Its applications in automation and predictive analytics have reshaped traditional workflows, paving the way for more efficient across multiple sectors.
Industrial AI begins: Curse or blessing?
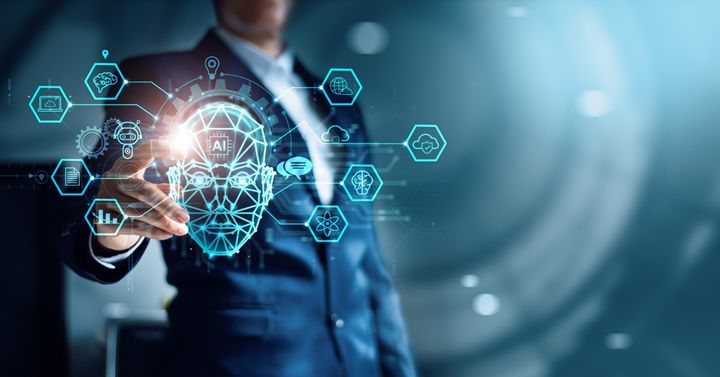
JOHANNES PETROWISCH | COPA_DATA
The rise of AI in manufacturing
Artificial Intelligence (AI) has emerged as a game-changer in the manufacturing industry. With its ability to analyze vast amounts of data and to make accurate assumptions as well as predictions, AI is transforming factories into smart, efficient production hubs. Adoption of AI is changing the manufacturing industry by making it much more efficient and better at controlling data and quality.
AI systems are designed to simulate processes such as learning, reasoning, problem solving, perception and decision-making. It involves various approaches – including machine learning, natural language processing, computer vision, robotics, and more – with the aim of creating machines that can emulate human cognitive abilities to some extent. The goal of AI is to enable machines to perform tasks autonomously, learn from data, adapt to new situations, and perform with a level of intelligence and efficiency that matches or exceeds human capabilities.
AI has the potential to revolutionize the manufacturing industry by improving efficiency, reducing costs and increasing safety. According to a recent report, the market size of AI in the manufacturing sector was valued at USD 2.3 billion in 2023 and is projected to reach USD 20.8 billion by 2028 (1). The AI market spans a wide range of activities, with areas such as supply chains, marketing, product development, research, analysis, and more expected to incorporate artificial intelligence into their business frameworks to varying extents.
Transforming manufacturing practices
How can production companies benefit from the use of AI today? Manufacturing companies that have embraced machine learning (ML) as a key part of their digital transformation efforts are now leading the way in the industry. They have adopted a range of cutting-edge technologies including artificial intelligence, big data analytics, machine learning, automation and predictive modelling. Collectively known as the Fourth Industrial Revolution, these technologies have delivered significant benefits in terms of cost reduction, increased efficiency and improved productivity.
A few numbers indicate the progress and pace of change:
- Almost half (49%) of advanced manufacturing and mobility companies have seamlessly incorporated AI-driven changes in their products or services into the process of allocating capital. These companies are actively investing in AI-driven innovation.
- By the year 2030, it is anticipated that 96% of companies will boost their investments in AI for manufacturing (2).
- According to a report by Accenture, Artificial Intelligence (AI) has the potential to boost labor productivity by a staggering 40% or more by the year 2035 (3).
- A survey conducted by McKinsey and Company revealed that the use of artificial intelligence in supply chain and manufacturing can lead to significant cost savings. The survey found that 64% of respondents saw cost reduction in the manufacturing space while 61% saw a reduction in supply chain planning costs (4).
AI will significantly change the manufacturing industry and create new job opportunities. The competitive advantage gained by using AI and ML will continue to grow over time, widening the gap between early adopters and those lagging behind in manufacturing (5).
Smart manufacturing with AI technology
AI and ML are playing an important role in the manufacturing industry. With the massive amounts of data generated by the Industrial Internet of Things (IIoT) and Smart Factories, AI solutions have emerged as powerful tools to effectively analyze and utilize this data. They aid in optimizing planning and sequencing, offering supply and demand forecasts, while also assisting in monitoring and control.
AI-fueled solutions help to accelerate the journey towards a Smart Factory, and all the opportunities and advantages related to it. This includes:
- Reduced costs: By optimizing processes and data management, you can effectively reduce operating costs through more efficient use of resources.
- Improved efficiency: Identify and address underperforming assets by analyzing the data generated by your Smart Factory. A Smart Factory adapts to demand, enabling more predictable inventory management. This minimizes downtime and maximizes productivity.
- Enhanced product quality: Smart manufacturing systems continuously monitor product quality for defects and detect trends, enabling you to make the necessary adjustments to achieve higher yield rates and improved customer satisfaction.
- Reduced production downtime: Smart manufacturing technology provides 24/7 monitoring of machine performance. Armed with this insight, you can proactively schedule predictive maintenance on equipment. This prevents breakdowns before they disrupt production.
Power of predictive maintenance in manufacturing
Anticipating and mitigating failures can result in substantial cost reductions and financial benefits. McKinsey claims that predictive maintenance represents the most impactful value of AI in manufacturing (6). But what is predictive maintenance?
In the context of maintenance, machines and plants are often subject to fixed cycles, which may suggest reliability and safety. However, experienced maintenance staff know that a fixed cycle may not always meet the requirements of day-to-day production, as it does not account for actual demands or pressures. Fixed maintenance that always takes place at the same intervals can result in components being replaced too frequently or even too late, leading to increased costs.
Predictive maintenance can help direct maintenance efforts to the actual needs, reducing costs and increasing productivity. Getting the most out of your equipment not only saves money but is also more sustainable.
Unlocking efficiency by empowering human operators
In manufacturing, AI can improve workflows by managing mundane and repetitive tasks that once had to be done by human operators. The system monitors and analyses complex machinery, sifting through large amounts of data to predict potential issues or breakdowns. This approach frees up human labor from routine checks and inspections, allowing individuals to focus on higher-value tasks that require human intuition, creativity and problem-solving skills.
AI is here to stay
The integration of AI in the manufacturing sector has transformed the industry, leading to more intelligent and efficient production processes. Companies that have adopted AI and machine learning have reaped significant benefits, including reduced machine downtime, improved productivity and decreased costs associated with quality issues. This technological synergy liberates human operators from mundane tasks, enabling a focus on more critical, high-value work that demands human intuition and problem-solving skills.
When it comes to the question of whether AI is a curse or a blessing for the manufacturing industry, the balance convincingly falls on it being a blessing. Advances in AI technology have paved the way for countless opportunities and potential benefits. While it is true that the nature of jobs may evolve and change, AI will ultimately enhance and expand human capabilities rather than reduce employment opportunities. The impact of AI in industry is undeniable and its potential to improve processes, increase efficiency and drive innovation is immense. Used responsibly, AI will be an extremely positive force that will continue to change and transform industries for the better.
To stay informed about the future impact of AI in manufacturing and to keep up with the latest industry trends, we encourage you to continue engaging with our blog. Discover further insights into zenon's contribution to digitalization here.
The content & opinions in this article are the author’s and do not necessarily represent the views of ManufacturingTomorrow
Comments (0)
This post does not have any comments. Be the first to leave a comment below.
Featured Product
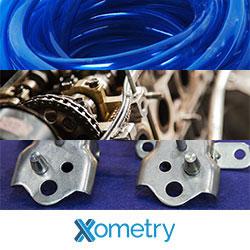