Many businesses are already using continuous monitoring technologies - like Internet of Things (IoT) connected devices - which is a good start; but the key lies in not just simply monitoring the output of various data (which is how many companies use it today), but by taking the next step and employing advanced algorithms and machine learning to take action from real-time insights and anticipate future outcomes.
Predictive Maintenance, the 1st Step Towards Self-Maintenance and AI
Kenneth Sanford | Dataiku
Today, predictive maintenance is widely considered to be the obvious next step for any business with high-capital assets looking to harness machine learning to minimise equipment maintenance costs. Predictive maintenance takes data from multiple and varied sources, combines it, and uses machine learning techniques to anticipate equipment failure before it happens.
Many businesses are already using continuous monitoring technologies - like Internet of Things (IoT) connected devices - which is a good start; but the key lies in not just simply monitoring the output of various data (which is how many companies use it today), but by taking the next step and employing advanced algorithms and machine learning to take action from real-time insights and anticipate future outcomes.
Going one step further, the most innovative enterprises, no matter what type of high-capital assets they maintain, see the largest cost savings from predictive maintenance not only by putting a system in place that returns simple predictive outputs, but by rethinking and optimizing their entire maintenance strategy as a whole from top to bottom. This means:
- Paving the way for artificial intelligence (AI) and self-maintenance by optimizing for (and automating) the immediate next steps once predictive systems point to imminent failure, whether this automatically triggers a work order, notifies a technician or certain team, places an order for a replacement part, etc.
- Considering a combination of maintenance strategies to determine the optimal cost-saving combination of predictive and traditional maintenance, perhaps even on an asset-by-asset basis.
- Identifying how to best execute necessary repairs through second-order or secondary analytics, meaning having a process in place for an entire deeper layer of analysis to determine the best time to actually remove the asset from service and which additional repairs - if any - should be conducted simultaneously to minimize the cost of having to remove the asset again for a different failure within a short window.
To get started, data science company, Dataiku, has published a free whitepaper “How To: Future-Proof Your Operations with Predictive Maintenance”outlining the steps every organization needs to embrace to make predictive maintenance effective within the short term and also to prepare for the long-term changes and benefits it can bring:
1. Understand the Need
The first step in moving toward predictive maintenance is to understand pain points (namely drivers of costs, waste, or inefficiency) and identify the best use case for your business.
2.Get Data
Of course, the proliferation of IoT plays a large role in predictive maintenance, especially with cheap sensors and data storage combined with more powerful data processing that has made the technology accessible. But, there are other data sources out there, which might include:
- Data from programmable controllers
- Manufacturing execution systems
- Building management systems
- Manual data from human inspection
- Static data, like manufacturer service recommendations for each asset
- External data from APIs, like weather, that could impact equipment conditions or wear
- Geographical data
- Equipment usage history data
- Parts composition
3. Explore and Clean Data
After identifying relevant data sets, it’s time to dig in. Ensure you really understand all the data you’re dealing with and that you know what all of the variables mean, what is being measured, and where all the data is coming from.
4. Enrich Data
Manipulating data at this stage means adding more features and joining it in meaningful ways so that each data set, or data from multiple sensors, can be taken as a whole instead of in parts.
5. Get Predictive
It is precisely this combination of a variety of sources and data types that allows for the most robust and accurate predictive models. The more sources and types of data available, generally the better the complete picture of a particular asset and the better the prediction.
6. Visualization
Visualization is an important tool in predictive maintenance as it often closes the feedback loop, allowing maintenance managers and staff to see the outputs of predictive models and direct their attention accordingly. Robust data science or data team tools today allow maintenance managers and staff on-the-ground to easily access and digest outputs in a familiar format so that the entire team - from analysts to technicians - receive the same feedback.
7. Iterate, Deploy, and Automize
Deploying a predictive maintenance model into production means working with real time data, but to iterate and deploy means providing visual real time dashboards for on-the-ground maintenance teams. For some use cases, feedback can be integrated directly into the predictive maintenance process, requiring no (or little) human interaction.
Secondary Analytics
Once it’s clear that a repair is necessary and initial first steps or processes have been kicked off, that’s where secondary analytics come in. he goal of secondary analytics following predictive maintenance is to determine a plan of action for exactly when the asset should be taken out of service so as to minimize disruption and loss (both imminent and future) and maximize resources.
Conclusions and Next Steps
The biggest initial win with predictive maintenance initiatives is cost savings. But after implementing a larger, more robust, and more mature predictive maintenance strategy, larger opportunities begin to open from a business perspective, and high-value assets can bring in some additional revenue instead of just being costs.
Predictive maintenance also lends itself to the future of artificial intelligence (AI), where operations will be entirely self-maintenance with very little human interaction whatsoever. AI in the predictive maintenance space would go one step beyond the steps discussed above, which would still require some manual analysis of models and outputs. These systems will watch thousands of variables and apply deep learning to find information that could otherwise be undetected that might lead to failure. Ultimately, predictive maintenance isn’t so far off from AI, and businesses that get started with predictive maintenance programs now will be well-poised as market leaders in the future.
To learn more about implementing predictive maintenance download the free whitepaper: “How To: Future-Proof Your Operations with Predictive Maintenance”
The content & opinions in this article are the author’s and do not necessarily represent the views of ManufacturingTomorrow
Comments (0)
This post does not have any comments. Be the first to leave a comment below.
Featured Product
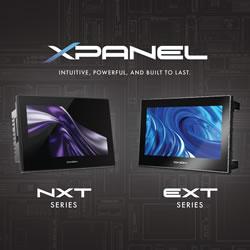