We have reached a tipping point to reengineer our end-to-end supply chains. Resilience across the entire value chain is critical. You must have the systems in place and ensure there is no over-dependence on any one partner, country, or region.
Accelerating Digital Transformation to Support Post-Pandemic Growth
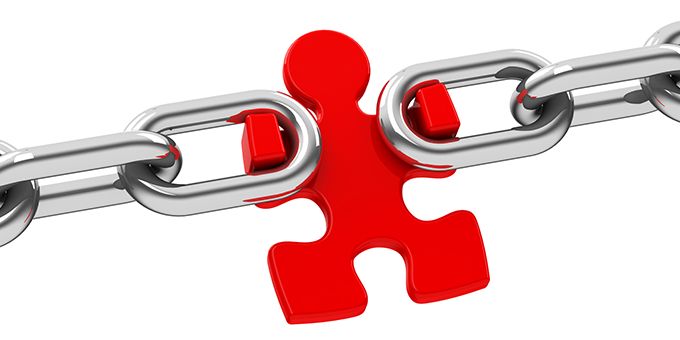
Q&A with Aurea Jimenez, VP of Indirect Procurement | Flex
Flex is the manufacturing partner of choice that helps customers design, innovate, build and deliver products that improve the world; our global operations serve nearly every industry, from automotive to communications and from healthcare to industrial and lifestyle, with over 160,000 employees.
My role at Flex is Global Indirect Procurement Vice President, including Strategy, Sourcing, Negotiation, and Supplier Management of all Goods and Services. I lead a Creative, High Performance, Multidisciplinary team of +350 persons who deliver Bottom Line Results and revolutionize Indirect Procurement to a Faster and More Intelligent Supply Chain Organization.
Indirect Procurement organization is structured in four teams: Regional centralized purchasing operations (Americas, APAC, EMEA, India), Global Commodity Management that handles global suppliers and procurement overall strategy, Center of excellence that is our navigator on KPIs and technology and last, but not least compliance which is fundamental in ensuring everyone is following our processes and procedures. A team of experts in several business categories, which include: Metals, Chemicals, IT, Facilities, Outside Services, MRO, Waste Management, and Business Travel.
What has Flex or other manufacturers done to mitigate the impact of the pandemic?
From the beginning of the pandemic, employee safety has been our number 1 priority. We quickly developed safety protocols and procedures, which include social distancing and the use of PPE. To ensure we were not impacting the supply of masks to frontline healthcare workers, Flex purchased equipment to make masks ourselves, and globally, we are now producing over a million masks a week. We have been able to supply our employees and their families with masks and donate some to local communities.
Besides, we have always strived to do the right thing and make a difference within our communities; for example, we invested in increasing Flex involvement with its customers to launch and speed up the assembly of medical ventilator programs out of which, we ended manufacturing quantities that surpassed previous industry volumes in record times.
What kind of risk can procurement help identify and prevent?
Every risk affects our supply chain; however, within the current market environment we live in, which is full of disruption, it is still a difficult job.
Managing every aspect of our supply chain: data, market, supplier, and customer relationships, risk management, amongst many other activities, will allow us to prevent any major disruption as much as possible.
How is procurement accelerating digital transformation to support post-pandemic growth?
Procurement is an area challenged to capitalize on digital transformation.
Flex has been investing in its digital tools for several years, and it has benefited the company greatly during the pandemic. Through our Pulse system, we are able to track all parts through the entire system. But you can't live on data alone. You also need supply chain experts to analyze the data and take action.
We have also made significant efforts to deploy aQuire, a Source-to-pay solution based on Ivalua's platform, where now we are in the final deployment phase.
Moreover, there are greater efficiencies to be gained in the procurement function: Digitally enabled collaboration with internal stakeholders and suppliers, automated/robotized processes, strategic partnership with suppliers, real-time data to make critical decisions immediately, and become more predictive.
How has procurement leadership changed as a result of value chain disruption related to COVID?
I would not exactly say that we have changed but instead evolved and adapted; we must understand that disruption globally would be a given and part of the new normal. Our Procurement and Supply Chain teams must develop paths to become more resilient.
Current market challenges have required us to expedite our processes to close the gaps. One of the things company should focus on is its supply base in order to always strive for continuous improvement to effectively compete with the world's best.
Looking beyond the pandemic, what are some of the lessons for the next crisis?
We have reached a tipping point to reengineer our end-to-end supply chains. Resilience across the entire value chain is critical. You must have the systems in place and ensure there is no over-dependence on any one partner, country, or region.
With the risks, challenges, and disruptions that organizations face every day, we should be ready to take on those to maximize resiliency proactively.
About Aurea Jimenez
Aurea has a degree on International Business, and within 20 years at Flex, has developed a career in several Supply Chain positions, currently as VP of Indirect Procurement. Indirect Scope covers Sourcing, Negotiation and Supplier Management of Goods and Services worth USD$2.4Bn Annual Spend. Aurea Leads a Creative, High Performance, Multidisciplinary team of +350 persons, that deliver Bottom Line Results, additionally to revolutionize Indirect Procurement to a Faster and More Intelligent Supply Chain Organization.
The content & opinions in this article are the author’s and do not necessarily represent the views of ManufacturingTomorrow
Comments (0)
This post does not have any comments. Be the first to leave a comment below.
Featured Product
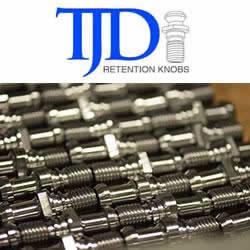