Companies that embraced digital technology, specifically on the plant floor, are now able to improve and adapt their operations at a faster speed and even anticipate changes before they occur.
Why Digital Transformation Matters More Than Ever
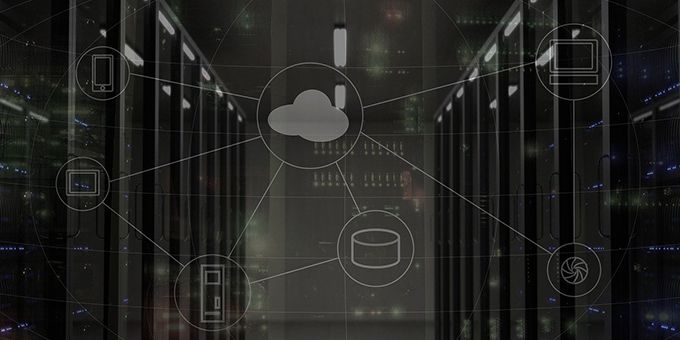
Jason Chester, Director of Global Channel Programs | InfinityQS
The digital landscape has been consistently changing for well over a decade and for manufacturers, it has been evolving at an increasingly rapid pace. According to Gartner, 91% of organizations are engaged in some form of digital initiative, yet only 40% have brought these initiatives to scale. The reason why some manufacturers have been at the top of their respective industries since the turn of the last century is because they have successfully adapted to their environment. Companies that embraced digital technology, specifically on the plant floor, are now able to improve and adapt their operations at a faster speed and even anticipate changes before they occur.
The drivers of digital change
It’s the responsibility of any manufacturer to conduct their due diligence and identify any threats that could impact their business. If done correctly, they will be able to prepare for most situations, however, as recent events have shown, there are some disruptions that can hit us without warning. These unexpected events have resulted in the business world moving away from a secure, safe and stable market, to one that has become uncertain, unpredictable and increasingly unique.
As technology has evolved, so has society, and with everything becoming increasingly connected, this has resulted in purchasing habits changing exponentially. The internet has meant consumers have now become both influencers and influences, and have a wealth of tools at their fingertips, such checking ratings, reviews, and the sources of the cheapest deals. As society has evolved, so have attitudes. Consumers are more sensitive to a myriad of different issues such as waste, pollution, sustainability, and climate change which now have a strong influence on their buying decisions.
These are huge challenges for manufacturers to overcome.
Add to all that COVID-19, which has caused unpredictability and volatility across entire value chains just as manufacturers have experienced a massive impact on workforce availability, restrictions to the workplace, and limitations to travel. This has occurred during a period in which global logistics and supply chains are tearing down barriers and cost-of-entry for new competitors, making the world much smaller for manufacturers and even more competitive. This is why it’s vital to adapt to change and transform.
Adaptation and transformation
The odds are stacked against any organization that refuses to embrace digital technologies and proactively transform in today’s market. So, what are the top five reasons that manufacturing needs to prioritize digital transformation initiatives now more than ever?
We need to do more with less
Given the current climate, it’s imperative that manufacturers have the infrastructure, talent, and capabilities to do more with less, either by reducing costs or being agile in the face of disruption. Some may work in an industry where demand plummets fast and this puts pressure on the business in terms of where they can cut costs. Others have seen demand skyrocket over a short period which requires quickly doing more with less. For these companies, even though demand has increased, they still have to navigate the disruption across the upstream supply chain.
While some manufacturers may not be at either sides of these massive swings in demand, rather they are somewhere in the middle where demand has been only modestly impacted to a greater or lesser extent. In any case, the need to do more with less is prevalent beyond that which is driven by demand. Manufacturers need to reduce waste, energy, and resource consumption, and become more sustainable, all while ensuring that production is safe, fit for purpose, and to the highest quality.
Increased operational agility
Adapting to volatility and uncertainty on both the demand and supply sides are critical. The rule book on demand forecasting and supply chain planning no longer applies as the current climate is too unstable to predict what demand will look like in the very near future.
To cope with this, it’s vital to be more agile and responsive. Manufacturers need to reduce the latency between when they start to see things happening across the market and make the decisions about what they do on the plant floor in response to that. The decision-making process must be reduced from weeks to days, if not hours.
Quality never sleeps
Although we are in the middle of a global pandemic, quality should never take a back seat. If manufacturers are making products that are not up to a high standard, then they will simply not be purchased or repurchased. Customers and regulators will still expect a high-quality and consistent product; therefore, quality should remain at the top of any organization’s list.
Tribal knowledge is a high-risk strategy
Tribal knowledge is all the experience that has been gained on the plant floor from years and years of manufacturing a product. Unfortunately, with manufacturers having to reduce their workforce, there are now fewer experienced employees on the plant floor, resulting in a gradual fading out of this valuable tribal knowledge. This is a huge risk for manufacturers and they will need to capture and convert that tacit tribal knowledge into explicit rules, procedures, processes, and workflows to ensure that they are consistently implemented.
Remote is the new reality
A year ago, it would have been unheard for a manufacturer to have the majority of their staff work remotely, but this is now the new norm. However, ‘remote’ doesn’t necessarily mean at home, it could simply mean working remotely from the plant floor while abiding by social distancing rules. For example, a productions supervisor would have to do their job from an office located on-site, rather than actually walking the factory floor, so it’s important to develop a system that will provide staff with safe and easy access to the data and analytics capabilities they need, without putting them at risk.
Overcoming new challenges
Digital transformation is the key in helping to address any new challenges experienced by manufacturers and data, and it is a great way for manufacturers to increase visibility into their operation through the centralization of all their data. This allows for greater analysis and can provide an important insight into each stage of the production process. The insights can then be leveraged to help business leaders make the right decisions which will be essential for their organization to secure long-term growth.
Keep your head in the clouds
Every few years a new innovation comes onto the market that completely changes the way organizations operate. Recently, this innovation has been the cloud and it is proving to be the best and most cost-effective solution for manufacturers to unify and centralize their infrastructure and operations. The cloud is easy to deploy, secure, remotely accessible, and functions in real time - hence why so many organizations have been able to allow their employees to work remotely for so long.
The cloud is constantly evolving and maturing, and as each day passes, it becomes more secure, powerful and innovative – it’s highly transformational. Manufacturers no longer have the excuse to say they don’t have the correct infrastructure to adopt the cloud, as the speed of deployment is quick and easy (just ask any organization who had to switch to the cloud in March to continue operating).
With many in the industry now seeing the critical importance of a proactive digital transformation, most manufacturers are taking it very seriously and embarking on their own initiatives. With the right strategy in place, this will help them to overcome the many challenges they currently face, survive any further disruptions, and prosper in the future.
1 https://www.gartner.com/en/information-technology/insights/digitalization
About Jason Chester
Jason Chester is responsible for the implementation, management, and overall success of the InfinityQS global channel partner programs. With over 25 years of experience working directly within the Enterprise B2B IT sector, Jason’s understanding of digital manufacturing technologies helps the company to deliver significant and sustainable business value to end-user organizations across the world.
The content & opinions in this article are the author’s and do not necessarily represent the views of ManufacturingTomorrow
Comments (0)
This post does not have any comments. Be the first to leave a comment below.
Featured Product
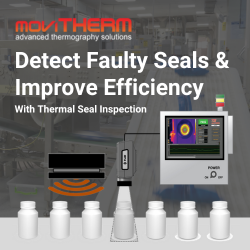