A downside of so much automation is that there is now a heavier dependence on machinery/robots to perform action. For some lines, if one of robot goes down, the entire line does.
Edge AI technology In Manufacturing Operations
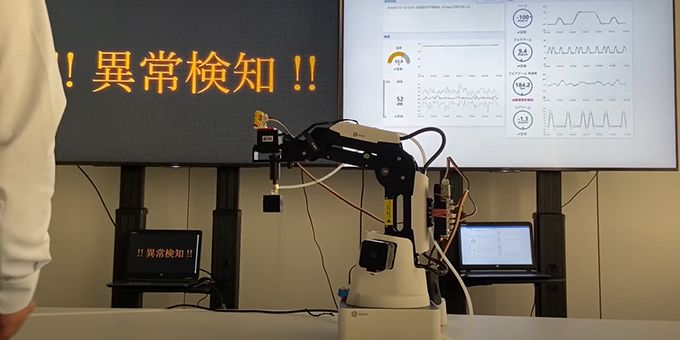
Q&A with Chris Catterton, Director of Solution Engineering | One Tech
Tell us about yourself and your role with One Tech.
As the Director of Solution Engineering, I lead of group of very bright-minded individuals who own the responsibility of crafting our technology to meet the needs of our clients. The Solution Engineering team gets involved with projects early on in the discovery phase to ensure that the architecture and functionality of the solution being delivered will provide value and have a positive impact to the business. We look at deployments differently than most technology vendors – we look at how our technology can integrate with existing systems, not just sit as a new data silo within the organization. Our solutions typically talk to multiple systems, pulling and pushing data to increase velocity within business operations.
What solutions does One Tech provide?
ONE Tech provides edge-based AI that is designed to be deployed on industrial assets, at their physical location. This product is called MicroAI™. Along with MicroAI, we have a platform with three levels of service offerings:
-
Helio One: A Predictive Maintenance and Operational Excellence platform designed to run in industrial environments. Helio One aggregates sensor data, PLC data and other data from sources to build a real-time profile of each piece of equipment on the line for operational insights. The benefit it drives is a deeper understanding, driven by AI, into the equipment behavior as well as overall productivity.
-
Helio Advance: Includes Helio One along with the ability for plant operations and maintenance personnel to have a real-time view of productivity KPIs for the entire line. The system runs AI analysis of operator behavior/cycle times, equipment cycle times and OEE along with cause/effect analysis on current events and inefficiencies with the recommendations on how to improve the productivity. All of this is visualized on role-based dashboards.
-
Helio Enterprise: Combines Helio One and Advance, while additionally offering workflow management tools for plant operations and maintenance to manage critical processes such as Workorders, Dispatches, Maintenance and Quality. The system is mobile app enabled for use by operators and technicians to understand what is happening on the line from the palm of their hand.
Given the increasing need for remote automation in manufacturing facilities, how is Artificial Intelligence (AI) device and equipment training at the edge a game changing technology?
Automation within manufacturing facilities has been widely adopted. This allows for less people to be involved in the manufacturing process. A downside of so much automation is that there is now a heavier dependence on machinery/robots to perform action. For some lines, if one robot goes down, the entire line does. This is where ONE Tech really shines. Detecting signs of failure on these assets prior to them causing unexpected downtime is what we do very well. This is accomplished by understanding what normal behavior of an asset is. The assets that we connect to range from fixtures and simple electric motors that power conveyor systems to large material handling robots and robotic welding arms with many points of failure. By understanding what a normal/healthy cycle for this machine is, we are able to detect anomalies and signs of failure within the equipment behavior.
The “edge” part of edge AI is important. Reason being, no two robots are going to be the exact same – they could be performing the same task but in different geographical locations with different climate/environmental pressures, they could be utilized at different rates, the list goes on and on in regards to why a unique model should be trained for each asset that is being monitored.
Is the Cloud still a key factor in gathering insight from an IoT-enabled device on the manufacturing floor? How do the cloud and edge work together to deliver the best results?
Industrial assets can produce a lot of data. Transmitting all raw data to a cloud could potentially be cost prohibitive. That being said, there is still a space for cloud technology to be leveraged. For instance, as data is processed at the edge locations, it can be shipped to a cloud environment for storage and further analysis. ONE Tech will soon release an update to our software with cloud AI functionality for users to run further analysis on their data. This will allow them to understand timing of certain downtime occurrence (e.g., after 600 cycles, robotic welder model x needs 3 more volts to continue operating at planned cycle time due to welding tip wear).
What are the security risks associated with this type of technology?
For some manufacturing facilities, keeping data local without transmitting to an external environment is the only option. This is usually due to data privacy and security concerns. ONE Tech has a security offering that utilizes a very similar algorithm used for predictive maintenance. The primary difference is that instead of looking at physical components of a machine, this security product looks at the internals of connected assets to detect anomalies which could indicate a possible malicious intent. Once detected, MicroAI can trigger a reboot of the device, a security ticket to be opened, or can simply cut network traffic to and from the connected asset. This version of MicroAI can be placed at multiple levels throughout a deployment – at the edge/asset level, along with up the stack at the database, application and network level.
Can you give us an idea on some of the barriers to entry for a manufacturer trying to implement remote automation?
Manufacturers are obviously focused on the ROI of implementing an innovative solution, such as remote automation and predictive maintenance. There are many factors – cost, time, which vendor to use, and simply where to start.
We simplify this process. We have a discovery call with the manufacturer to identify a particular line that has lower than expected overall equipment effectiveness (OEE). We gain an understanding of which assets are on the line and deploy a Proof of Concept, or as we like to refer to them at ONE Tech, a Proof of Benefit. These usually last a couple of months and the return on investment is realized by the manufacturer. From the PoC phase, we create a very transparent roadmap of the time and cost associated with rolling out the solution across more lines and facilities.
Share a real-world example of how AI device training at the edge can benefit a manufacturer on an assembly line.
We are working with multiple automotive facilities where unexpected downtime leads to low OEE. Primarily, the lines that we work with are heavily dependent on robotic welders and robotic material handlers. Our process is quite simple. We identify existing intelligence that we can pull from the line (i.e., data from PLCs/controllers, Manufacturing Execution Systems, internal sensors from the OEM, etc.), and aggregate with additional sensors that are placed on the machines to create a 360-degree view of the asset and its vital components.
MicroAI aggregates data from existing intelligence along with additional sensors placed on the equipment and a model is created through a training process that is formed by monitoring multiple cycles of normal operation for each style/part that the machine is responsible for working on. This is where horizontal analysis comes into play – if there are models created that look like outliers compared to the other, similar robots, that are created, we are able to adjust those models if needed. Once the models are in place, we begin processing the data. At a very simplistic level, our algorithms look for anomalies within the data. When these signs of failure are detected, MicroAI triggers an action. This action could trigger an API call to open a workorder within an existing workorder management tool or trigger flashing an alert on a monitor on the shop floor alerting to the machine/station that needs attention.
Our solutions are giving manufacturers advanced warning on items that could potentially cause unexpected downtime. This leads to corrective action taking place prior to the downtime occurring.
How do you see this technology evolving and gaining traction?
Cutting cost and improving output of existing equipment is the name of the game for manufacturers. Automation and having a forewarning for assets that are showing signs of failure prior to them going down has its obvious advantages. The technology that enables this is now here, and it’s being proven. It’s only a matter of time before this becomes status quo and manufacturers that don’t adopt this technology will be left behind the competition.
How have you seen COVID-19 affect manufacturing?
Manufacturing facilities are now starting to get back up and running. COVID-19 has been an eye-opening event that has manufacturers now realizing the importance of continuing to innovate. In some instances, manufacturing facilities that had automation in place prior to the pandemic, were able to start operations back up sooner due to safe social distancing that could be implemented. That being said, less personnel on the line meant that there was a heavier dependence on the equipment to perform properly. Being able to know when a machine was going to have issues, prior to the issue occurring is key to keeping operations running smoothly.
About Chris Catterton
Chris Catterton is the Director of Solution Engineering at ONE Tech. Located in Dallas, Texas, Catterton has over 10 years of experience deploying global enterprise software solutions- primarily in the space of Industrial IoT, Business Process Automation and AI.
The content & opinions in this article are the author’s and do not necessarily represent the views of ManufacturingTomorrow
Comments (0)
This post does not have any comments. Be the first to leave a comment below.
Featured Product
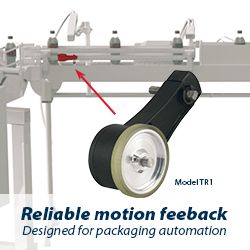