How POSCO is addressing market obstacles and protecting its vital steel production assets from corrosion.
Excelling in Today's Challenging Global Steel Marketplace
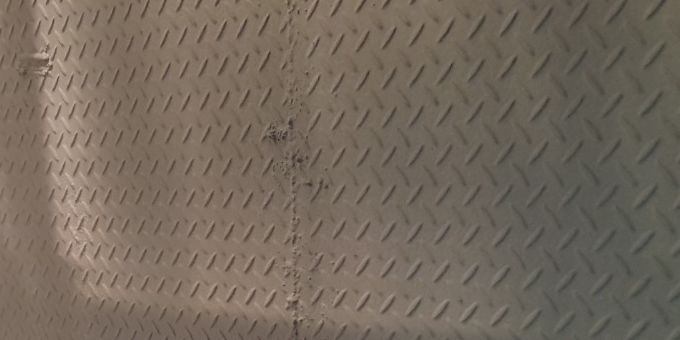
Del Williams | EonCoat
After the global steel industry’s recent downturn, caused by oversupply, low prices, and rising raw material costs, Pohang, South Korea based POSCO, one of the world’s largest multinational steel manufacturers, needed a strategy for handling such challenges while continuing to protect their assets and remaining industry innovators.
By focusing on high value-added products, reducing cost, and innovating its product and process POSCO posted a double-digit operating margin and a jump in stock price of over 50 percent in 2016, according to its annual report.
Now the company – which won the world’s most competitive steelmaker competition for the eighth consecutive year in 2017, as announced by World Steel Dynamics (WSD), the world’s leading steel industry analysis agency – is poised to make further gains with innovative products and processes that will transform the industry.
One key initiative POSCO is pursuing involves a unique approach to protecting its massive carbon steel production and infrastructure assets from corrosion. This is a continual challenge for steel manufacturers globally, particularly along coastline exposed to high humidity and salty air. The company is utilizing an innovative coating that provides a long-term solution to fighting atmospheric corrosion and corrosion under insulation (CUI). The coating not only helps to minimize required maintenance and production downtime, but also promotes environmental health and safety, which is one of the company’s key missions.
Protecting Critical Steel Assets from Corrosion
Because steel mills require sufficient raw product in order to produce, they are often located near marine terminals where both raw material and finished product can be easily shipped.
As such, steel mill processing equipment and infrastructure must be coated to withstand atmospheric corrosion from the high humidity and salty air. It must also resist corrosion under insulation (CUI), which can result from exposure to moisture from sources such as steam, wash downs, sprinkler systems, or frequent condensation and evaporation of atmospheric moisture.
However, when traditional barrier type coatings are commonly reapplied every few years in such coastal areas, this can increase maintenance cost and production downtime.
To protect its steel assets from corrosion for decades, as well as improve environmental health and safety, POSCO turned to EonCoat, a spray applied inorganic coating from the Raleigh, North Carolina-based company of the same name.
Before and after EconCoat treatment
EonCoat provides two layers of protection for POSCO’s steel assets. First, unlike conventional barrier coatings that only physically cover the surface, it forms an alloy layer that chemically bonds with the surface of the steel. This effectively prevents intrusion from moisture and other corrosion promoters. EonCoat also forms a ceramic outer layer that further resists corrosion, water, abrasion, impact, chemicals, and high temperatures.
According to Sungjun Ahn, Senior Manager from Dong Buk Chemical, the company in charge of the application process at POSCO, EonCoat was selected to extend equipment life in accord with POSCO’s sustainability and environmental management policies.
“POSCO stakeholders benefit, including investors, when they can safely extend the lifespan of their steel assets with less maintenance,” says Ahn. “Without frequent repainting, they can more productively invest in further product and process innovation.”
At the Pohang steel plant, the spray applied inorganic coating is being used to protect a variety of equipment such as storage tanks, boiler dust collectors, and dock pilings (including the splash zone and below the waterline).
Due to the coating’s high temperature resistance of up to 500 Celsius, it is also being used in high temperature areas of the steel making process, such as at the ends of steel rollers and for pipeline insulation.
Because of the coating’s unique inorganic properties, it is very effective at stopping CUI, which can affect pipeline or vessels beneath insulation due to water penetration.
Since the coating is also chemical resistant, it is also being considered as a primer for equipment in contact with sulfur dioxide (SOx) and nitrogen dioxide (NOx) gasses, which result from burning fossil fuels and smelting mineral ores.
More Innovative Processes
While taking a proactive approach toward preventing corrosion, POSCO utilizes a number of advanced steel producing technologies at its two South Korean steel mills, in Pohang and Gwangyang, including:
Finex: This eco-friendly iron making process allows the direct use of cheap iron ore fines and non-coking coal as feedstock. Compared to a traditional blast furnace process, this significantly lowers operating cost and emissions as well as dramatically reduces overall construction costs by eliminating the need for sinter and coke plants.
Strip Casting: This method eliminates the slab-making process to produce hot-rolled flat products directly from molten iron. Compared to traditional slab-making, this technique reduces cost, energy use, and production time as well as pollution.
Endless Hot Rolling: This solid state joining method is a rolling technology that joins bars made from slabs, the material for hot-rolled products, for endless rolling. Compared to previous rolling processes, this method drastically cuts production time while economically offering firmer, thinner steel plates.
Game Changing Products
With such advanced steel producing technologies in place, supported by a preventative approach toward corrosion, the company has recently introduced some important product innovations. This includes super-high-strength “Giga Steel” – which can withstand more than 100 kg of load per 1 mm2 with a tensile strength of 1.5 Giga – produced at its Gwangyang Steel Mill in Korea.
Since the tensile strength, measured by pulling the steel plate from both ends until it is torn, is greater than 1 gigapascal (GPa), a unit of force, it was dubbed Giga Steel. As such, a palm-sized (10 cm X 15 cm) piece of Giga Steel can support the weight of 1,500 1-ton semi-mid-sized cars. The unique material will enable building significantly lighter, stronger vehicles since it is over three times stronger than aluminum and has excellent formability.
At the company’s Global R&D Center in Songdo, Korea a new Steel Forming Laboratory will evaluate the formability of newly developed steel products such as the Giga Steel, and will include the use a 2000-ton hydraulic press to evaluate the formability of large components such as automobile side-outers. An existing Steel Forming Laboratory will also evaluate the basic physical properties of steel required by customers (forming, welding, coating, corrosion and fatigue) and provide support such as quality certification.
Protecting Health, Safety, and the Environment
Along with meeting steel industry challenges with product and process innovation, the company also takes seriously its commitment to the health and safety of its workers and the environment.
According to Merrick Alpert, President of EonCoat, “Our company is extremely proud to help POSCO further their eco-friendly processes and products that contribute to sustainable global development.” As part of environmental management, POSCO has sought to improve the air quality near the steel works and surrounding areas by reducing the total emission of air pollutants including dust, NOx, SOx and VOCs.
Since the coating is inorganic and non-toxic, there are no VOCs, no HAPs and no odor. This improves health and safety and helps to mitigate the negative effects of air pollution.
The coating consists of two non-hazardous components that do not interact until applied by a standard industrial plural spray system like those commonly used to apply polyurethane foam or polyurea coatings. This means the inorganic, non-flammable coatings can be applied safely even in confined spaces.
“POSCO’s use of the inorganic coating is part of their drive to innovate in the steel marketplace,” concludes Ahn. “It is helping them meet their commitment to benefit all stakeholders including investors, customers, employees, as well as the local and global community.”
The content & opinions in this article are the author’s and do not necessarily represent the views of ManufacturingTomorrow
Comments (0)
This post does not have any comments. Be the first to leave a comment below.
Featured Product
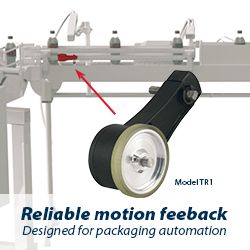