For years, the shop floor as been an island of its own and with the latest climate from the US government and other countries, more companies are seeking integration and connection to the corporate world.
Machine Data Collection and Monitoring
Greg Mercurio | Shop Floor Automations
Please tell us a bit about Shop Floor Automation?
Shop Floor Automations (the Automations is plural in our name) has been around since 1998. Our main office is in southern California, in San Diego County, but our services stretch all throughout America. We even service parts of Canada and Mexico. In a nutshell, we provide software and hardware solutions to manufacturing shop floors to help decrease downtime and improve OEE. We help those working on shop floors gain extra time, productivity and profits.
If you could describe it in laymans terms, what is machine event/utilization monitoring?
So let’s clarify – we call it machine data collection and machine monitoring. Event is more trigger-based, like on something happening via an operator on the machine, but it doesn’t necessarily have to be event-driven. I wouldn’t use that word. In a basic term, machine monitoring is a way to measure the productivity on the shop floor that allows manufacturers and executives to make informed decisions based on what processes are happening. This way, they can streamline the process, reduce downtime, etc.
Why is machine monitoring important? Why should it be viewed as a crucial necessity instead of a luxury purchase for a shop floor?
Going with the advantage of machine monitoring, not only is the efficiency being monitored, but also the ability to make informed decisions. Knowing that something is wrong hours later may affect the total job and output. So if the operator can tell them quickly that “we’re having issues with the tooling”, they can communicate that while the machine is stopping. A machine isn’t useful when it’s down.
What is your best laymans description of MTConnect? Correlate how it meshes with machine monitoring.
The MTConnect Protocol is an open-source, royalty-free communication method to deliver the analytics to an off-the-shelf product, like we sell. Ideally, MTConnect is going to speak English, if you will, to all the different types of equipment that is in the shop, versus saying there are proprietary islands that are each different and have to work with multiple vendors to get different subsets of data off the machines. If we give one solution through MTConnect, they can take all that data to streamline it back to the source of data analytics through Predator, Scytec or off-the-shelf monitoring systems. There’s a new device coming soon called the Multi Connect, which can integrate with old and new types of machines, and use the MTConnect Protocol specifically, which is exciting.
In an interview you did with another publication back in November of 2013, you said that most shops run only at about 60 to 65 percent machine utilization. Has that percentage increased over the past three years, now that machine monitoring has had more of a presence?
There have been more inquiries over the last few years, since that interview, with machine monitoring being a bigger topic, these days. Also, with the push behind MTConnect, I think shops are looking to streamline productivity, solutions, and integrating. Before, I think it was too cost prohibitive – there were vendors out there that were selling proprietary software that made it expensive and it was only them being the source. Now, with the Multi Connect, I think it’s going to change the game, as far as pricing and at the same time, more people are asking about it because the companies they are competing with for the jobs are also doing this.
In attending IMTS and FABTECH last year, you had lots of visitors. How has the number of leads increased from those shows and how would you say their concerns have changed since you last attended them? Has their collective interest grown in machine monitoring?
At IMTS, there were more vendors than ever before issuing machine monitoring. One of the newest concepts is cloud-based, subscription-based solutions. A lot of the vendors right now that are popping up are these new companies that have the ability to interconnect with these pieces of equipment through Ethernet, but they lack in the ability to integrate with the latest machines. So we have this breadth of products that allows them to do that. Because there are these new machines and this new technology, these companies are popping up left and right. They don’t have what we have, as far as solutions, hardware, and also our 19 years of experience.
What is your understanding of Industry 4.0 as it relates to your business and the industry in general?
Industry 4.0 is here. Our clients are asking for more data and more awareness of what is happening on the shop floor. We are providing solutions using software and new products, like the Multi Connect, to bridge the gap between machines. For years, the shop floor as been an island of its own and with the latest climate from the US government and other countries, more companies are seeking integration and connection to the corporate world.
Manufacturing is getting a lot of attention due to the political climate in the US. How do you see that playing out over the next 5 years?
I think we’re going to be very busy in 2017 and hope that’s a trend that will build as time goes on. We are supporters of organizations like AMT and events like MFG Day, so the Made in America movement is important to us.
Greg Mercurio is President of Shop Floor Automations. He is a long time resident of San Diego County and a family man. Shop Floor Automations will soon be celebrating two decades in business.
The content & opinions in this article are the author’s and do not necessarily represent the views of ManufacturingTomorrow
Comments (0)
This post does not have any comments. Be the first to leave a comment below.
Featured Product
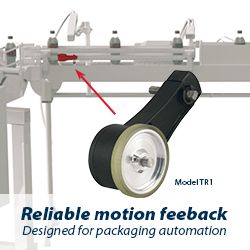