How Robotics Has Helped The Manufacturing Industry
The future is now. In fact, the future has been “now” for quite some time. What was once mere science-fiction is now put into practice every day. Robotic automation is all around us. It is part of our daily routine. There is no escaping it.
Few industries have been impacted more by the advent of robotics than the manufacturing industry. In fact, the manufacturing industry was one of the first to implement robotics all the way back in 1961.
Since then, science-fiction has become a normal part of life. Let’s take a look at how robotics has become an indispensable asset to the manufacturing industry.
Eliminating Danger
One of the first uses for robotics in the manufacturing industry was to take dangerous jobs out of the hands of humans. Robots can pour molten metal liquid into a cast for automotive manufacturing saving the lives of humans and reducing the need for time-consuming policies to be put in place.
Efficiency and danger go hand-in-hand.
Today, robotic arms are also used to handle radioactive materials in nuclear power plants and dangerous chemicals in chemical manufacturing plants.
Even in a warehouse setting, robots now have their undeniable place. Dangerous pallets that would take 3 or 4 men to lift could be moved with safety and ease with the help of robotics.
Increased Efficiency
Robots don’t get tired as humans do. Nor do they become afflicted by a lack of enthusiasm for their tasks or illnesses. Robotic manufacturing machinery can be programmed to handle precise tasks over and over again and they won’t ever lose motivation or need to take a break.
While a robotic apparatus is just like any machine that needs maintenance and mechanical attention, it can work non-stop, for the most part, meaning continuous automation.
It is not subject to fatigue and can, therefore, increase manufacturing output by a tremendous margin!
Saving Human Talent
Taking menial tasks out of the hands of the human workforce has also been beneficial for the manufacturing industry. While robotics has come a long way, there are still creative tasks, critical thoughts and executive decisions that can only be handled by humans.
Freeing up precious manpower by assigning the mindless or menial work of industry to robots adds an indispensable human asset to manufacturing businesses.
Addressing Shifting Interests
You would be hard-pressed to catch a millennial saying “I want to work on a manufacturing line!” Young people are shying away from manufacturing jobs but the industry still needs to go on, and still remain an important part of our daily lives.
Robotics has addressed this shifting trend away from manufacturing jobs by filling them with machines.
In fact, manufacturing would have taken a huge hit over half a century ago if not for robots stepping in and filling the positions that have become less and less attractive to humans.
Cost-Efficiency
And of course, there is the economical factor. A manufacturing line that would need 20 people to operate could increase output by installing two or three robots. They would not incur any overtime either. In many instances, robotics helps manufacturers operate for less and get tasks done in shorter times.
The tale of scientific advancement is inseparable from the narrative of the industry. And the relationship between the two will only become more enmeshed as time goes on. Now, through this article, you can see how important robotics is to the manufacturing industry.
About the Author: William R. Bennett is a polyurethane specialist for TPC Inc based out of Southern California, and looks to help leaders of industry find the best solutions for their manufacturing and production needs.
Comments (0)
This post does not have any comments. Be the first to leave a comment below.
Featured Product
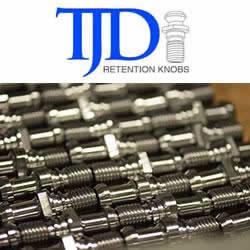