Computer scientists design flat sheets that transform themselves into smooth-surfaced, free-form objects
Phys.org: 3D printers have been around since the 1980s, but we are still far from maximizing their potential. One active area of research and development is "self-actuating" objects: flat materials that transform themselves through material forces into the desired 3D object. Previously, however, the range of objects was limited to those with sharp edges and little, if any, curvature, and the transformation methods were based primarily on folding or processes that could not be controlled very precisely (e.g. chemical reactions or inflation). Now, for the first time, a group of current and former IST Austria computer scientists have made it possible to create self-actuating, smooth, free-form objects. In so doing, they developed both an ingenious material design and a new method of self-transformation—they call the fruits of their innovation "CurveUps". Moreover, the team, which consists of Ruslan Guseinov, Eder Miguel, and Bernd Bickel, developed the computational tools to take a user-provided 3D model and automatically create a 2D flattened template that, upon release, transforms into the original 3D version.
The goal of the project was ambitious in a number of ways. First, it is very challenging to obtain a final 3D object that is mechanically stable. Moreover, the team had to develop a controllable mechanism to accomplish this. "I experimented with so many different materials and methods before coming up with our current design," says first author Ruslan Guseinov. CurveUps are made up of tiny tiles sandwiched between pre-stretched latex layers. During the transformation process, the tension in the latex pulls the tiles together joining them into a continuous shell.
An innovative design and transformation method were only part of the team's contribution, however. With these ideas in hand, the team focused on developing tools to create the 2D templates for printing. In particular, their program takes a user-supplied 3D form, and automatically generates a 2D tile layout, including the orientation, location and shape of each tile and connecting pins. However, as even small models will have hundreds or thousands of individual tiles, this represents an optimization problem of tremendous proportions—infeasible, on any personal computer. To get around this, the group implemented a two-step optimization procedure, which first gives an approximate solution, then performs local refinements before producing a final template. Full Article:
Comments (0)
This post does not have any comments. Be the first to leave a comment below.
Featured Product
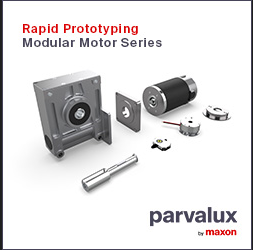