With Tacton we wanted to give users the flexibility and configuration options they need to outfit their facility, while ensuring the system was reliable, secure, and easy to install.
Edge Computing and AI in Manufacturing
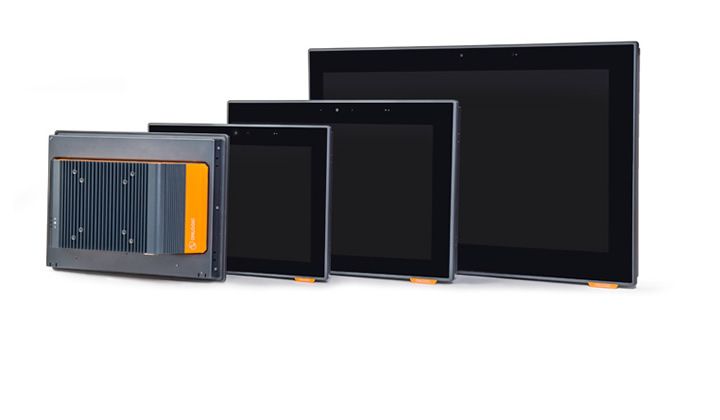
Q&A with David Zhu-Grant, Product Management Lead | OnLogic
Tell us about yourself and your role at OnLogic.
I'm the Product Management Lead at OnLogic. We're a global manufacturer of industrial computing solutions for the edge. I have nearly two decades of experience in helping deploy technology solutions in harsh environments, and lead the team responsible for identifying, vetting and positioning the products that help the world's most innovative companies overcome their computing challenges. I get a lot of joy out of finding ways to use technology to solve real-world problems that help individuals and businesses grow and succeed.
OnLogic has been creating solutions for the manufacturing industry for decades now, can you talk about why your hardware is such a good fit for manufacturers?
The most obvious thing that has attracted manufacturers to OnLogic over the years is the design of our hardware. Manufacturing facilities are notoriously tough on technology so we engineer our computing solutions to resist damage from the challenging environments they'll be installed in.
-
Fanless and ventless enclosures help prevent ingress from airborne particulates, including dust, wood or metal shavings, flavoring or coloring powders, or anything else that might be floating around in the air at a production facility.
-
Advanced thermal management design, and components with wide operating temperatures, helps reduce performance throttling in hot and cold environments.
-
Limited internal cabling, combined with vibration isolation elements, help to prevent damage to systems installed on a manufacturing line, or on mobile equipment like forklifts.
-
Thoughtful design decisions and special gasketing help to combat electrical interference, which is of increasing concern as production facilities implement more and more technology that relies on wireless communications.
-
Our dedicated regulatory team ensures that our systems are thoroughly tested to relevant industry standards in manufacturing, automotive, medical and railway applications (just to name a few) which can help get users up and running quickly and more affordably since they don't have to do all that testing themselves..
In addition to the quality and capabilities of the hardware, at OnLogic we focus on helping manufacturers overcome challenges. Rather than just being a vendor for hardware, we enjoy partnering with our customers to make sure their projects succeed. We want to know what they're trying to achieve, and how we can best help them optimize their facilities and/or products. Identifying the right hardware solution can be challenging in a sea of similar looking offerings, so when we have the chance to really chat with businesses about what they're trying to do, that's when we get excited and can work with them to piece together the right combination of hardware, software partners and services to make implementation as straightforward as possible.
Share with us some of the key challenges you've been helping customers overcome recently?
Access to, and visibility of, edge data is something we talk to so many customers about. The rise of AI has made balancing workloads throughout a facility even more challenging, so making sure systems are connected and communicating effectively is vital. But all that data is useless if you can't see it and effectively interact with it.
To help address these challenges, we recently launched a new line of rugged panel PCs and industrial displays called Tacton, and the response has been incredible. The feedback we've gotten over the years from hardware users was invaluable in developing these new systems. In addition to reliable data access and machine control, other key challenges that Tacton addresses include ease of installation and mounting as well as physical access control and data security. Balancing performance, connectivity and cost is such an important equation to solve for manufacturers and we truly relish the opportunity to help customers on their digital transformation and optimization journey.
Tell us more about Tacton and what makes it special?
With Tacton we wanted to give users the flexibility and configuration options they need to outfit their facility, while ensuring the system was reliable, secure, and easy to install.
On the customization side, in addition to being able to choose from a range of 12th Gen Intel processors, as well as memory and storage options, we also integrated our ModBay™ expansion technology, which allows users to choose from a selection of additional connectivity options, including more LAN, COM, or USB.
The displays themselves are also really outstanding, and come in 18 different versions depending on the use case. Users can choose a resistive or projected capacitive display, regular or high brightness, and from 3 different sizes ranging from 12 to 21.5 inches. There's an onboard proximity sensor that can turn the screen on when approached, and an optional front-facing camera. The front bezels are rated for ingress protection of either IP66 or IP69K depending on the screen configuration, and the capacitive screens are optically bonded for enhanced clarity.
In terms of longevity, the specs really speak for themselves, but the system is able to operate in extreme temperatures, has wide-power input, and was tested to withstand vibration and shock. We even went as far as creating our own patented panel mounting clips for Tacton. We'd heard from customers that some panel mounting clips would vibrate loose over time, and even fall off in some installation environments that are subject to frequent vibration. Tacton's mounting clips screw on easily and have a locking ring that holds the knob in place once installed. It's that level of attention to detail that we think users will really be able to feel with Tacton.
As factories become smarter and more connected, why is the computer and processing power so important to keep up?
For one, more devices means more complex workloads and more risk should systems fail or become overtaxed. Updating hardware regularly ensures that facilities can keep pace with innovation and the competition. The jump in performance and capabilities from a 7th or 8th generation Intel processor to a 12th generation CPU is night and day. In addition to the raw computational power increase, modern CPUs have so many built in security, graphics, and AI capabilities that simply weren't available just a few years ago. The i3 in Tacton is on-par with an i7 or i9 processor from only a few years ago.
Can you talk a bit about AI Hardware and Edge AI? What are they and why is it important for a manufacturer to understand these?
AI hardware is a broad term for any computing hardware that can leverage AI software. Edge AI is the implementation of AI capabilities at the edge of the network, closer to where the data is being produced, rather than in the cloud. Our VP of Edge Solutions recently wrote a great article on the subject that I'd encourage everyone to check out, but there's certainly huge potential for manufacturers to leverage AI for process optimization, product cost analysis and improvements, inventory management and so much more. We're still in the early stages of turning the promise of AI into real cost savings and ROI, and there are a lot of moving parts, which is why we have a dedicated team that works with customers interested in implementing AI solutions at their facility. Now is the time for manufacturers to consider how AI could help them, but it can be intimidating, so we created an AI crash course, which includes a 6-step guide to getting started with AI.
Look into the future a few years, where do you see Edge Computing and AI in manufacturing and how is OnLogic leading the way?
Looking out a few years I believe we will see AI more ingrained in industries that may not have previously even considered it. Some of this will be out of pure necessity in order to remain competitive, and some of it will be to optimize and improve performance when considering key challenges, such as labor shortages and new processes with legacy systems/equipment. I think a specific trend we will continue to see is more compute moving to the edge, with more on-premise compute being implemented as the cost of the enterprise cloud at scale becomes prohibitive. The edge can really help by enabling intelligent insights analysis and decision making to happen right where the data is being generated, rather than needing to send, store and process it in the enterprise cloud, all of which adds to the total cost of ownership of these industrial systems.
Here at OnLogic we have very close alignment with our partners, like Intel, and are very much leaning into empowering the edge through AI and our reliable hardware solutions. One area we are specifically working on is looking at compute as a spectrum which ranges from on-CPU processing, to dedicated acceleration such as onboard NPUs or external accelerators, through to onboard Integrated GPUs (iGPU) and, of course, discrete GPU (dGPU). These different options for compute all offer different levels of performance, size, power consumption and cost, and from an AI perspective OnLogic is paving the way for customers to right-size their needs, not just sell them a highest performance GPU if it’s not needed. In this way we provide reliable, flexible edge AI systems as well as access to a network of partners that help support implementations of all sizes.
The content & opinions in this article are the author’s and do not necessarily represent the views of ManufacturingTomorrow
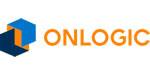
OnLogic
OnLogic is a global industrial computer manufacturer who designs highly-configurable, solution-focused computers engineered for reliability at the IoT edge. Their systems operate in the world's harshest environments, empowering customers to solve their most complex computing challenges, no matter their industry. OnLogic has helped more than 70,000 customers worldwide advance their ideas with computers that are designed to last, built to order and delivered in days.
Other Articles
How to Choose the Best Industrial Small Form Factor PC
Acquiring Accurate Measurements in Manufacturing with Mate Gauge
How to Choose the Right Edge Computer
More about OnLogic
Comments (0)
This post does not have any comments. Be the first to leave a comment below.
Featured Product
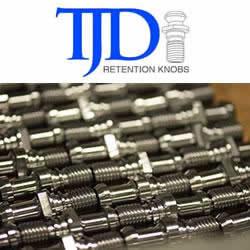