Nexa3D Launches xCure Intelligent Post Processing System for Consistent Part Performance at Production Scale
● Unlocks full photopolymer production potential using validated workflow ● Delivers consistent mechanical part performance every build ● Accommodates multiple build plates or single parts of up to 16 liters in volume ● Features dual wavelength LEDs and prescribed parallel UV and thermal modes
Ventura, CA, October 19, 2020 -- Nexa3D, the maker of ultrafast polymer production 3D
"We are very excited to bring xCure to market, underscoring our commitment to deliver fully validated workflow solutions for manufacturing at scale," said Avi Reichental, Co-founder and CEO, Nexa3D. "Our work with key manufacturing companies and leading material suppliers reveals that only through the rigorous development, simulation and testing of predictive and prescriptive end-to-end workflows can we unlock the full range and consistency of mechanical performance."
In addition to its prescriptive material specific capabilities and larger chamber size, xCure is simple and intuitive to operate with its single click, rotate, and push operation, offering maximum curing cycle efficiency and full part surround coverage. With dual 365+405 nanometer wavelength LEDs and optional thermal curing, xCure delivers the full spectrum of Nexa3D's resin curing coverage with validated resin specific pre-sets that ensure consistent part curing results print after print. Six strips provide 360° of light and thermal coverage with a reflective interior for optimal uniformity and maximum functionality.
xCure is the latest in a series of Nexa3D's new product introductions, including high-performance polymer materials xCE-Black and xCE-White as well as xClean, a highly effective eco-friendly washing solvent for all resin-based 3D printers. Along with the company's flagship printer, the NXE400, Nexa3D enables customers to strengthen their design agility and supply chain resiliency by compressing their design and manufacturing cycle, effectively reducing the time required to produce functional prototypes and production parts from hours to just minutes.
About Nexa3D
Nexa3D makes ultrafast industrial grade polymer 3D printers affordable for professionals and businesses of all sizes. The company's printers are powered by proprietary Lubricant Sublayer Photo-curing (LSPc) and Quantum Laser Sintering (QLS) technologies that increase print speed and productivity sustainably by orders of magnitude. The company's partnerships with world-class material suppliers unlocks the full potential of supply-chain approved performance polymers that are tailored for faster prototyping and volume production applications. The company's end-to-end validated workflows are designed to maximize productivity by reducing 3D printing cycles from hours to minutes and sustainability by minimizing waste, energy and carbon footprint. To learn more, visit www.nexa3d.com.
Featured Product
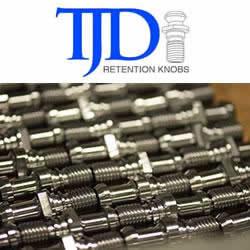
T.J. Davies' Retention Knobs
Our retention knobs are manufactured above international standards or to machine builder specifications. Retention knobs are manufactured utilizing AMS-6274/AISI-8620 alloy steel drawn in the United States. Threads are single-pointed on our lathes while manufacturing all other retention knob features to ensure high concentricity. Our process ensures that our threads are balanced (lead in/lead out at 180 degrees.) Each retention knob is carburized (hardened) to 58-62HRC, and case depth is .020-.030. Core hardness 40HRC. Each retention knob is coated utilizing a hot black oxide coating to military specifications. Our retention knobs are 100% covered in black oxide to prevent rust. All retention knob surfaces (not just mating surfaces) have a precision finish of 32 RMA micro or better: ISO grade 6N. Each retention knob is magnetic particle tested and tested at 2.5 times the pulling force of the drawbar. Certifications are maintained for each step in the manufacturing process for traceability.