According to a recent report from Boston Consulting Group (BCG), “Quality 4.0 Takes More Than Technology,” nearly two-thirds of manufacturers believe that Quality 4.0 will significantly affect their operation within five years.
Quality 4.0 Takes More Than Technology
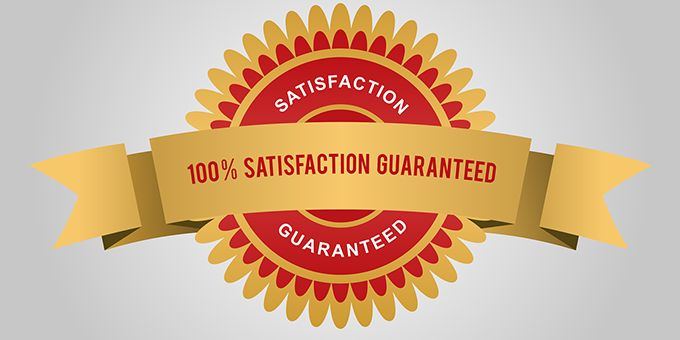
Q&A with David Isaacson | ETQ
According to a recent report from Boston Consulting Group (BCG), “Quality 4.0 Takes More Than Technology,” nearly two-thirds of manufacturers believe that Quality 4.0 will significantly affect their operation within five years. However, only 16% say their company has begun implementing Quality 4.0 practices and 63% have not even reached the planning stage yet.
What is Quality 4.0?
Quality 4.0 is complementary to the concept of Industry 4.0, which classifies the technologies – such as machine learning, predictive analytics, IoT, artificial intelligence, social media, big data and cloud computing – that are changing the way manufacturers develop, manage and maintain quality standards throughout the manufacturing process. Quality 4.0 defines the approach manufacturers take when infusing new technologies with traditional systems for managing quality – such as quality management system (QMS) software – to drive continuous improvement and improve overall business performance. What are the key enabling technologies behind Quality 4.0?
The key technologies used in a Quality 4.0 approach typically mirror those enabling Industry 4.0. However, while new technologies are important for adhering to the digital era, manufacturers must first have a formal quality management strategy in place that incorporates highly intuitive and comprehensive QMS technology solutions. Otherwise, they will not have the foundation required for Quality 4.0 success.
The exact technologies manufacturers integrate with QMS tools when embarking on this journey will also depend on factors such as the goals they hope to achieve and the existing level of quality maturity within the organization. For example, a food and beverage manufacturer might want more accurate insights into the temperature of dairy products to ensure they remain between 34-38 degrees Fahrenheit throughout the manufacturing process. To accomplish that goal, the manufacturer might install IoT devices throughout the assembly line to automatically send data to a QMS platform. This data would instantly inform the Quality Managers of exactly when and where that temperature was not maintained, allowing them to take appropriate actions to adjust the production line.
How can a Quality 4.0 approach help manufacturers enhance business performance?
Quality 4.0 solutions enable organizations to inform business strategies more accurately than ever before, while solidifying quality as a positive driver of business performance. The integrations involved in this approach help automate and simplify traditionally time-consuming, manual business processes. In fact, BCG’s report states that improving business performance is the number one reason organizations plan to adopt Quality 4.0.
Quality 4.0 can help address quality problems preemptively, reduce response rates to quality errors and/or changes in market trends, improve regulatory compliance and enhance brand reputation. Through real-time process monitoring, data collection and predictive analytics, manufacturers can further solidify quality as a positive driver of business performance.
Is it costly to implement a Quality 4.0 strategy?
There is no set price tag on implementing a Quality 4.0 approach. The cost depends on the level of quality processes and tools manufacturers have already adopted, as well as the unique technologies that will best help them achieve their goals.
What might be stopping manufacturers from implementing a Quality 4.0 approach? What are the risks or challenges that technologies like the IoT present?
Manufacturers implementing Quality 4.0 must first establish themselves as quality-minded and quality-driven organizations. To master quality and improve upon it with new technologies requires deep-rooted changes – from infrastructure to skillsets – that build and nurture a culture of quality within the organization.
These onboarding processes can seem daunting to manufacturers and prevent them from implementing a Quality 4.0 approach. In fact, BCG’s report cites that the number one challenge associated with Quality 4.0 technologies is the shortage of digital skills and talent, followed by having an unclear or lack of digital strategy and not having an existing culture of quality.
With foundational QMS solutions, each of these barriers can be easily overcome. Specifically, manufacturers should look to build their Quality 4.0 approach on QMS solutions that are user-friendly, come equipped with simple training programs, can help identify clear business goals and enable seamless quality culture.
What are the first steps a manufacturer needs to take in order to embark on a Quality 4.0 journey?
The first step manufacturers should take depends on which stage they are at in their quality journey. Based on how we’ve seen our customers evolve and establish a mature level of quality, we’ve developed four stages manufacturers can use as guidance when embarking on their own Quality 4.0 journey.
The first stage, called Ignite, is when manufacturers first identify why quality matters to them, and pinpoint internal quality challenges. Then, by the end of the first stage, they should be able to set several measurable outcomes.
The Accelerate stage of the journey comes next, when a manufacturer can begin addressing issues by optimizing quality processes and integrating with key stakeholders to enable seamless process flows between functions and systems. During the completion of the Accelerate stage, manufacturers have identified and assessed risks, minimized defects and delays, and can release new products quickly.
Many manufacturers currently reside at either the first or second stage in their quality journeys. However, there is a huge opportunity to advance beyond early stages quickly and efficiently, thanks to Quality 4.0.
When manufacturers make it to stage three, the Expand stage, they have begun building a culture of quality around their own best practices and continuously improving the entire supply chain ecosystem (including internal infrastructure, external suppliers and customers). This stage of the journey depends heavily on the solidified integration between people and the emerging technologies associated with Quality 4.0.
In the final stage, Transform, manufacturers should have met their goals and established themselves as quality leaders that will consistently improve. In this stage, it is assumed that Quality 4.0 has been integrated at all levels of the organization and the focus will shift toward quality harmonization throughout the entire ecosystem. Manufacturers should also be able to fully leverage the available data and advanced analytics processes introduced by new technologies and see real, measurable results.
All four stages are unique to the manufacturer and are dependent on the level of their quality maturity goals. Creating a culture of quality does not happen instantly, though, and each organization needs to first determine where they are on the path to seamless, impeccable quality.
What other cultural and organizational changes should manufacturers consider as they take a Quality 4.0 approach?
Beyond the technologies introduced in Quality 4.0, it takes people to ensure quality standards are met and consistently improved upon.
To build a culture of quality throughout an organization, and make managing quality seamless, manufacturers must empower all employees and stakeholders to prioritize maintaining quality on a daily basis. Training employees on the importance of quality and what it means to the company and to them personally aids in getting buy-in across the organization. User-friendly, automated QMS systems allow manufacturers to achieve this goal, by enabling them to devise and execute more agile, flexible and robust quality management strategies that engage and empower employees at every level to leverage key data that drives business decisions.
Incentive programs, that encourage employees at all levels and across functions to report quality data for a reward, can also be successful in building a culture of quality.
How can a manufacturer measure the results of this program?
Measuring the success of Quality 4.0 programs varies per manufacturer. However, the overarching goal is to simplify business processes and reduce costs.
Many manufacturers gauge quality success by eliminating scrap waste and defective products completely from the production process, both internally and with suppliers. Other measurable outcomes include increase in satisfied customers, a reduction in recall investigations and resolutions, minimized delays in shipping products, as well as avoidance of potential fines and penalties for non-compliance.
Can you share examples of how manufacturers have successfully approached Quality 4.0?
As indicated by BCG’s report, many manufacturers are still very early on in developing and pursuing their Quality 4.0 initiatives. However, some organizations have taken significant strides to enhance their quality management strategies and set themselves up for success once they’re ready to fully embrace this new approach.
For example, Lumileds, the global leader in light engine technology, has been able to establish itself as a quality leader by investing in and fully leveraging ETQ’s Reliance platform. Beyond reducing quality management costs, the QMS solution has helped the company build a culture of quality that can now be seamlessly found throughout every single brand touchpoint. In fact, Sadiq Eshaq, Technical Project Manager of Business Transformation Process, called Lumileds’ culture of quality “the backbone of the company” in a recent ETQ case study. He says that now, after implementing ETQ Reliance, “many of the decisions the company makes are based on quality, in terms of the suppliers we choose, and the customers that choose us base their purchase decisions on the quality of products that we create.”
With this mature level of quality, Lumileds is one organization that is clearly prepared to reap the benefits of Quality 4.0.
If you like this article you may like "Predictive Analytics vs Machine Learning"
The content & opinions in this article are the author’s and do not necessarily represent the views of ManufacturingTomorrow
Comments (0)
This post does not have any comments. Be the first to leave a comment below.
Featured Product
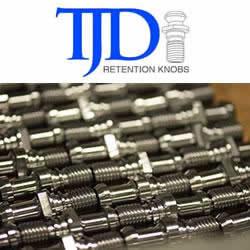